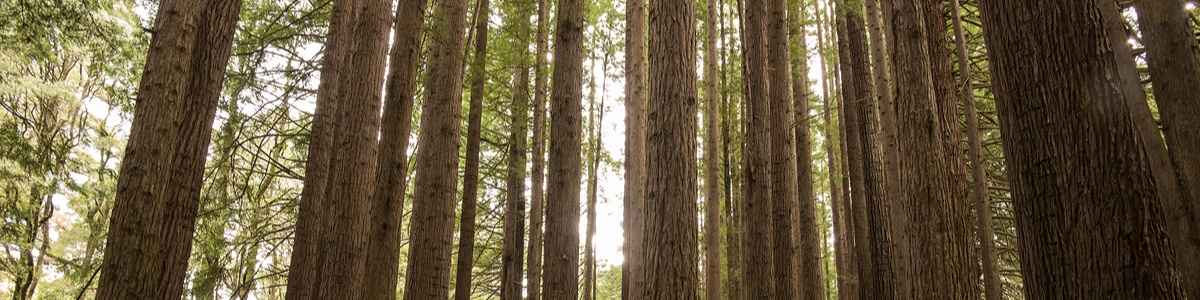
Jul
A more in depth look at Cellulose Fibre
What is Cellulose Fibre? Is it for you? In this post, we take a more in-depth look at Celluose Fibre and its applications in youe home.
Product Description
Cellulose Fibre is a grey-coloured fibre insulation made from recycled newsprint and cardboard. It is treated with inorganic salts, borax and boric acid, and is dry- or wet-sprayed into the area being insulated. Cellulose Fibre is manufactured locally in Brisbane. The Cellulose Fibre is made to the Australian Standards. The product is 100% fire resistant and exceeds the highest of Australian building codes. Cellulose fibre is 100% non-toxic, non-irritant, safe to handle and allergy free.
In most domestic applications Cellulose Fibre is the most effective insulation on the market. Cellulose fibre has gained its reputation worldwide and is fast becoming the popular choice product. With its loose fill properties and market leading efficiencies, cellulose fibre can block up to 100% of all temperature transference by ensuring no gaps in the installation. We stand behind our products giving our Cellulose Fibre an unprecedented guarantee against vermin, insects, fire and movement for the lifetime of the structure.
Cellulose Fibre is recognised internationally as premium environmentally friendly insulation. American and Canadian Institutes have done extensive comparative studies with regards to household thermal insulation products. The following facts are some of the reasons why it has earned such a high ranking with many international councils including the US Green Building Council. These studies have identified cellulose fibre as the premium insulation product.
Throughout this page we refer to overseas standards and test, primarily Canadian and American. This is because Australian insulation standards and building codes are in their infancy when compared to the level of study and the corresponding investments that cooler climate countries have undertaken. North American climates can experience extremes of temperature differences between summer and winter, which can be as high as 50 to 60 C°. This means that the thermal performance of a home is of high concern and this is reflected in North American building codes.
A quick overview:
Thermal performance of a residence is dependent on three primary factors.
Thermal resistance . The ability of a structure to inhibit the temperature movement between zones of differing temperatures. Insulation materials are installed into the structure to increase thermal performance and is measured in R Values. It is restricted only to the size of the cavity and the structures load bearing rating. With regards to a cellulose fibre the correct R rating is achieved varying the thickness and density of the insulation thereby adjusting its thermal resistance. For example 110mm at 30kg per cubic metre in density will give an R 3.00 and 128mm will give an R3.50. This principle is reasonably well understood in Australia. See R value table for a complete range. Note that American R values are not the same as Australian.
Air Tightness. Is ability of a structure to prevent air movement between zones of differing temperature. Although related this is independent of the performance of thermal resistance. Air Tightness is measured in air changes per hour. Most cold climate homes outside of Australia are required to have an air tightness value of less than three. A typical new Australian home will measure greater than 8 air changes per hour. 200% higher than the equivalent American home. Air Tightness is NOT understood well in Australia and Australian building codes are of low standard when it comes to air tightness. An easy to understand real life scenario is how air moves into and out of ceiling spaces via down lights, short circuiting any insulation that has been installed into the ceiling space.
This air movement if heated or cooled is rapidly lost from the building envelope using up more energy than a structure with a lower air tightness value. This is a very common scenario not well controlled by our current build codes. North American and European building codes require down lights to be installed in such a way that they maintain the air seal between the living area and the ceiling cavity. Furthermore it is preferably that down lights are sealed and preferably insulated to maintain the integrity and performance of the in-ceiling insulation.
Cellulose fibre has a very high performance with regards to Air Tightness which will is further explained below in greater depth.
Moisture Barrier. As Air Tightness performance increases moisture movement is restricted which may allow the build-up of moisture within the building structure. A semi per permeable barrier is installed to allow moisture transfer inter-zone to prevent this occurring. This is generally not a consideration in Australia as this relates to high Air Tightness values which are not found in Australian structures. It is presented to give a complete picture of how thermal performance works and to show how far Australian standards lag behind other countries.
How Green is Cellulose fibre insulation? Cellulose fibre is one of the most green friendly insulation products on the market for the following reasons.
Recycling Paper
Paper products make up to 38% of western land fill and as the fibres in paper break down the greenhouse gas methane is produced. By recycling 1 ton of paper not only can we reduce the greenhouse gas methane but it saves 3 cubic meters of landfill, 17 trees of lumber, 25 000 litres of water, 1500 litres of oil and reduces air pollutants by 95%.
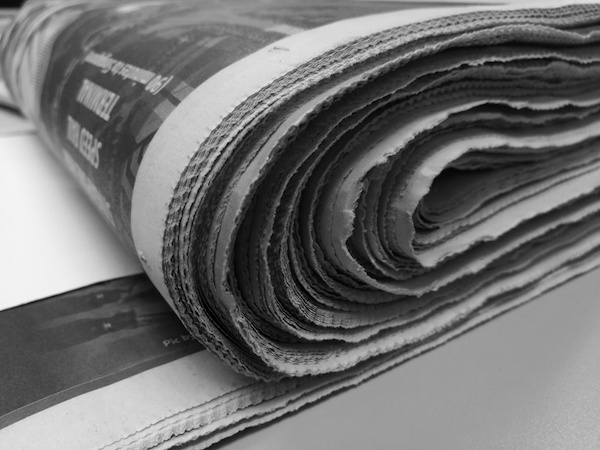
Embodied Energy
Embodied Energy is the sum of the total energy invested in producing a product . This includes energy in producing the raw product, a major component of this is energy from burning fuel in machines. EG Transport trucks, service vehicles, personal vehicles driven to work by employees, ECT. Another is the energy in manufacturing the product , primarily electricity typically produced by oil or coal burning power stations and lastly the energy to deliver the product which again has primary and secondary energy components. The primary being fuel used by the transport system and the secondary being the energy used by the supporting business. EG Electricity and petrol.
Fibreglass type products has at least 10 times the embodied energy when compared to cellulose fibre with the petroleum based foam insulation 64 times that of cellulose.
This coupled with its great thermal resistance and real life installed air tightness values and the associated energy cost makes Cellulose Fibre a very GREEN product.
Ceiling Insulation
Cellulose fibre insulation product is usually installed by professional tradesmen and will usually via the roof to the correct depth (according to Manufacturers specifications) providing you the correct required rating, giving you an insulation solution above recommended levels. Because the product is pumped in it is able to cover spaces that other insulations may miss. All roof types are catered for and handled with care and expertise including difficult, raked, exposed beam and standard roofs. Cellulose fibre can be installed at varying depths enabling it to provide a wide range of R-values across an even wider scope of applications than most other insulation product. Cellulose insulation performs just as well in ceiling as it does in wall for exactly the same reasons. Installed in ceiling cavities it fills all cavities, nooks and crannies, providing exceptional thermal and acoustic properties plus has great air tightness in comparison to most other competitive products.
In wall Insulation
Cellulose insulation is pneumatically blown into wall cavities filling all in wall cavities completely leaving no voids sealing electrical wires, pipes ECT. and density. Using specifically designed blower machines cellulose fibre blocks are broken up and combined with air at the correct ratio of air to product and blown to the installation point via flexible tubing. A fine mist of water is added at the nozzle end to help bind the insulation in place.
When combined correctly cellulose fibre acts more like a fluid, due to its particle size and density, and can be blown in and around pipes and wiring. It also fills cracks that develop between plaster board and the timber frames forming itself perfectly to that cavity. This fills and seals all gaps and cavities providing very high thermal and air-tightness performance. The gaps between the timber frame and plaster board develop over time due to wood shrinkage as timber gives up moisture over time. This means in wall cellulose fibre easily meets its R rating regardless of the installation constraints.
Batts on the other hand are inserted into the wall cavities with their edges stapled to the inside framing and compressed around wires, pipes, electrical outlets, etc. They are pre-cut a to a specific size and cannot accommodate all the subtle variations caused by building tolerances, warping of timber frames caused by building construction methods and products.
This can produce air pockets or voids throughout the wall cavity, causing thermal shorts and reducing its actual real life performance dramatically lower than the expected R- value. A study conducted by the National Research Council of Canada, (website http://www.nrc-cnrc.gc.ca ), found that the R-value of batts degrades by 14% to 35% due to voids or areas around pipes, wires, electrical outlets. A US study conducted by the National Association of Home Builders (NAHB), found that homes insulated with fibreglass batts lost 46% of their R-value due to voids.
Air Tightness’ or Building Envelope
One of the most important characteristics of insulation is the degree to which they air tighten the house envelope to stop air leakage.
Air flow moving through or around insulation will drastically reduce its thermal performance. Therefore, insulation products should be dense or tight enough to slow heat loss by convection, but not so dense that the insulation material actually conducts heat through it. A 1979 study conducted by the Oregon Department of Energy found that houses insulated with cellulose tighten the house by 15 to 20% over fibreglass. Blower door tests, equipment that measures air loss from a home, have consistently shown that homes insulated with cellulose insulation change 20% - 30% of their volume of air every hour compared to a change of 65% - 75% for homes insulated with fibreglass. As stated earlier air movement across temperature zones reduces thermal performance.
Analysis of actual real life installations regularly show that cellulose insulated buildings may use between 20% to 40% less energy than buildings with fibreglass, even if the R-value of the insulation in the walls and ceilings is identical. One reason for this is the capacity of cellulose to stop air movement due to its unique particle size and density. The fibres of cellulose insulation are much finer than mineral fibre blowing wool preventing air movement.
Acoustic ratings
The acoustic rating is measures in Sound Transmission Units abbreviated to STC and is the measure of insulations ability to absorb sound energy through a structure. IE wall or ceiling. Cellulose fibre insulation reduces sound transmission through the ceiling and walls better than most other thermal insulation of the same R rating. STC ratings are calculated in laboratory conditions and may or may not achieve these ratings in real life installations. In the case for cellulose fibre STC ratings are easily achieved for the same reasons that cellulose fibre excels in air tightness and fire resistance and that is its ability to resist void formations and air movement.
Again the reverse is true for batt and blanket products as acoustic shorts are easily introduced through the same voids and holes that reduce its thermal and air tightness ratings.
Product – same R rating and test conditions |
STC Rating |
Cellulose | 41 |
Polyester Batts | 35 |
Fiberglass or Mineral Fiber batts | 38 |
Icynene | 37 |
Fire Resistance - Cellulose makes your home safer!
Cellulose fibre has greater fire resistance than cellular plastic insulants. Boron additives enhance the natural fire resistance to comply with BS5803 Part 4:1985 (Methods of determining flammability and resistance to smouldering) when installed in accordance with BS5803 Part 5:1985 (Specification for installation of man-made mineral fibre and cellulose fibre insulation).
Product testing specifications
Product | Heat Evolution (0-10) | Ignitability Index (0-20) | Smoke Index (0-10) | Spread of Flame (0-10) |
Cellulose Fibre | 2 | 18 | 3 | 0 |
Most residences contain large amounts of wood in their structure. Cellulose insulation is most likely the only wood based building material treated with a fire retardant you will find in your home. This makes cellulose insulation one of the safest materials used in home construction. In a fire situation the dense structure of cellulose with its fire retardants stall the spread of flames and hot gases to other parts of the building, restricting the availability of oxygen in insulated walls and ceilings.
Studies by the National Research Council Canada have found that" cellulose in the wall cavity provided an increase in the fire resistance performance of 22% to 55%." The same council found that "the fire resistance of an assembly with glass fibre insulation was slightly lower than that of a non-insulated assembly. Other test have found that cellulose in a wall increased fire resistance 26% to 77%, as compared with an uninsulated wall.
Many fire test have been conducted, one of which you can view via this You Tube link in which cellulose insulated structures remained standing 50% longer than a fibre glass insulated structure. This gives occupants more time to escape in house fires and provides fire fighters more time to save the structure. Most fibreglass have been found to have little or no resistive fire value and has a low melting point typically melting away to nothing before the actually flames reach the insulation.
Insulation has had “bad press” over the last few years with regards to fire resistance both in Australia and internationally.
In reality most insulation related fires have been directly associated with overheating down lights. Upon investigation it is generally found that there was no relationship between fire incidents and any insulation products. Further Canada’s NRCC found that fibreglass slightly reduced a structures resistance to fire while cellulose increased the resistance between 22% and 55%. This in part is due to cellulose fibres quality of reducing drafts and air movement preventing air from moving inter-zone greatly reducing the amount of oxygen available to support combustion. Also the borates in the fibre allow a surface crust to develop which prevents further smouldering. This crust prevents the fire from penetrating further into the building frame.